A three phase motor is a machine that converts electrical energy into mechanical energy using three alternating currents of the same frequency. It is also known as a three-phase AC induction motor. It is more efficient than a single-phase electric motor, as it can transmit a larger volume of electricity at the same cost. The motor is made of two parts: a rotor that turns, and a stator that produces the magnetic field that makes it turn. The rotor is connected to the shaft of the motor, and the stator is made of three pairs of coils evenly spaced around it.
When connected to a three phase AC power supply, the coils in the stator set up a moving magnetic field that spins continuously. These moving magnetic fields create a current inside the rotor that lags slightly behind the magnetic field. This out-of-sync current causes a mechanical force that pulls the rotor around in circles, constantly trying to catch up with the moving magnetic field in the stator.
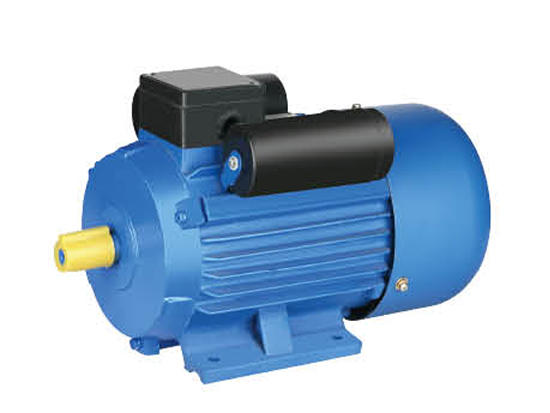
Three-phase power systems are used because of their inherent properties. The phase currents cancel each other out, resulting in zero current flowing on the neutral conductor on some lines, while others experience large currents that can cause fires and damage equipment. Three-phase electric power transmission is also more economical because it is possible to remove the neutral conductor on some lines, reducing wiring and distribution costs.
One of the first things to check when troubleshooting a three-phase motor is the supply voltage. If the supply voltage is significantly lower than the rated input voltage on the nameplate, it can cause issues with motor speed and torque. The voltage can be measured with a multimeter and compared to the specifications on the motor’s nameplate.
The voltage is then converted to a three-phase current by the inverter. This three-phase current is then fed to the motor windings. The windings are shorted by end rings to cut off the rotating magnetic field and induce currents in the rotor conductors. These induced currents are based on the principles of electromagnetic induction and Lenz’s Law, generating a mechanical force that turns the rotor.